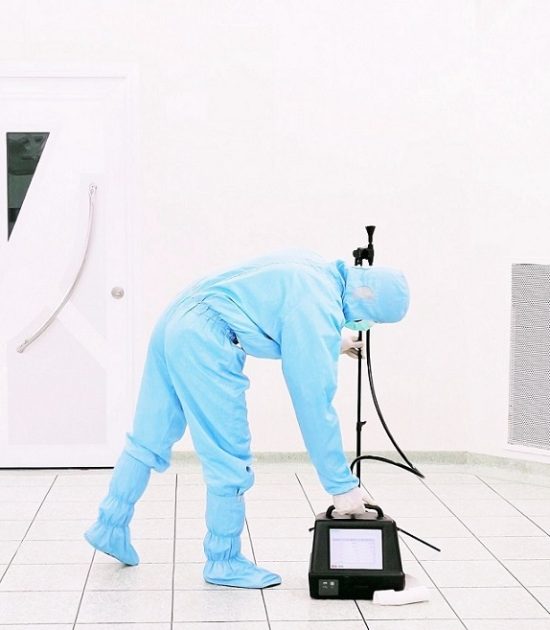
METING EN KWALIFICATIE VAN CLEANROOMS [NEN-EN-ISO 14644-1]
- Ventilatiecapaciteit / hoeveelheid luchtverplaatsing per ruimte
- Luchtsnelheid onder het filter (kamers met laminaire stroming)
- Integriteit van het HEPA-filter
- Aantal deeltjes volgens NEN-EN-ISO 14644 -1
- Hersteltijd kamer
- Drukverschil tussen kamers
- Rooktest
- Luchttemperatuur en relatieve vochtigheid
- Kooldioxidegehalte van de lucht
NEN-EN-ISO 14644-1 (beschrijving van de methodologie voor het meten van de hoeveelheid deeltjes in de lucht) en NEN-EN-ISO 14644-3 (beschrijving van de andere meetmethoden die bij de validatie van cleanrooms worden gebruikt) zijn normen die algemeen worden gebruikt voor cleanroommetingen in vele industrieën – farmaceutische, medische, laboratorium- en automobielindustrie. Bij de kwalificaties die wij uitvoeren, maken wij gebruik van de huidige edities van NEN-EN-ISO 14644-1 en NEN-EN-ISO 14644-3. Wij vergelijken de meetresultaten met de acceptatiecriteria die in de ISO 14644-serie normen, EU GMP-eisen of klantrichtlijnen zijn gespecificeerd. Maak gebruik van onze meetdiensten!
VOORGESTELDE OMVANG VAN DE TESTS
CLEANROOM: ISO KLASSE 7-9
[IN OVEREENSTEMMING MET
NEN-EN-ISO 14644-1]
Deeltjesgrootte (volume van elk monster: 28,3l)
Hersteltijd kamer
Drukverschil tussen kamers
Luchttemperatuur en relatieve vochtigheid
CLEANROOM: ISO KLASSE 5-6
[IN OVEREENSTEMMING MET
NEN-EN-ISO 14644-1]
Deeltjesgrootte (volume van elk monster: 1m3)
Hersteltijd kamer
Drukverschil tussen kamers
Luchttemperatuur en relatieve vochtigheid
LAMINAIRE FLOWKASTEN (LABORATORIUM/INDUSTRIËLE SCHAAL)
Integriteit van het HEPA-filter
Luchtsnelheid onder het filter
Deeltjesgrootte (volume van elk monster: 28,3l/1m3)
Rooktest
OPTIONELE TESTS VOOR CLEANROOMS
Ventilatiecapaciteit / hoeveelheid luchtverplaatsing per ruimte
Integriteit van het HEPA-filter
Rooktest
Kooldioxidegehalte van de lucht
TECHNISCHE VOORSCHRIFTEN VOOR GESELECTEERDE TESTS
CONTROLEREN ALVORENS TE BESTELLEN
Ventilatiecapaciteit / hoeveelheid luchtverplaatsing per ruimte:
We gebruiken de balometermethode.
Ventilatormaat: 610mm x 610mm (standaard). Neem
contact met ons op als u een andere roostermaat heeft.
Capaciteit rooster: 80 - 3500m3/h.
Plafondhoogte: maximaal 3,5m.
Integriteit van het HEPA-filter:
Vereiste opening voor het inbrengen van de testaërosol (vóór filter): 13mm diameter.
Vereist 230V stopcontact (vóór het filter): op maximaal 25m afstand.
Vereiste opening voor de concentratie van de testaërosol (vóór het filter): 10mm diameter.
Vereiste verwijdering en installatie van het filterdeksel door de klant (schone zijde).
Vereiste levering van een werkplatform door de klant indien het filter zich op een hoogte van >2,5m bevindt.
RAPPORTAGE
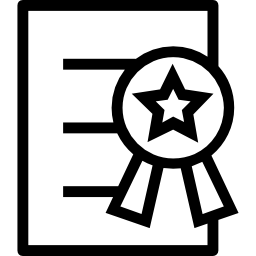
IN OVEREENSTEMMING MET DE
GMP-NORM
De resultaten worden op afzonderlijke testbladen (IQ/OQ/PQ) geplaatst. Het rapport bevat onder meer de identificatie van de gebruikte apparatuur, de personen die aan de tests hebben deelgenomen.
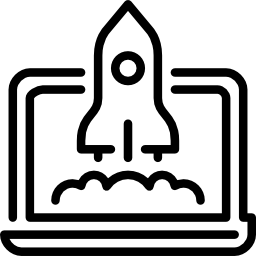
KLAAR BINNEN
14-30 DAGEN
Standaard stellen wij het rapport op in het Engels.
Wij sturen het rapport doorgaans binnen 14 dagen
(maximaal 30 dagen) na de meting.
HEBBEN ONS AL VERTROUWD
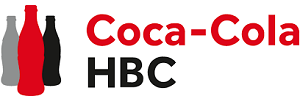
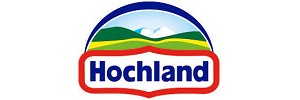
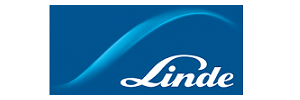
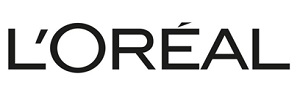
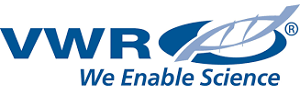
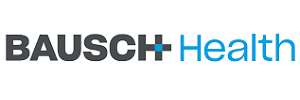
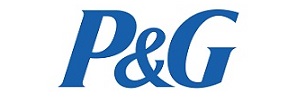
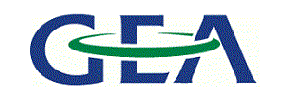
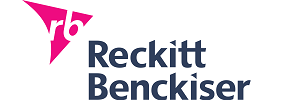
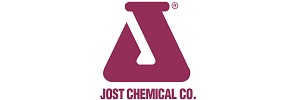
ONS TEAM
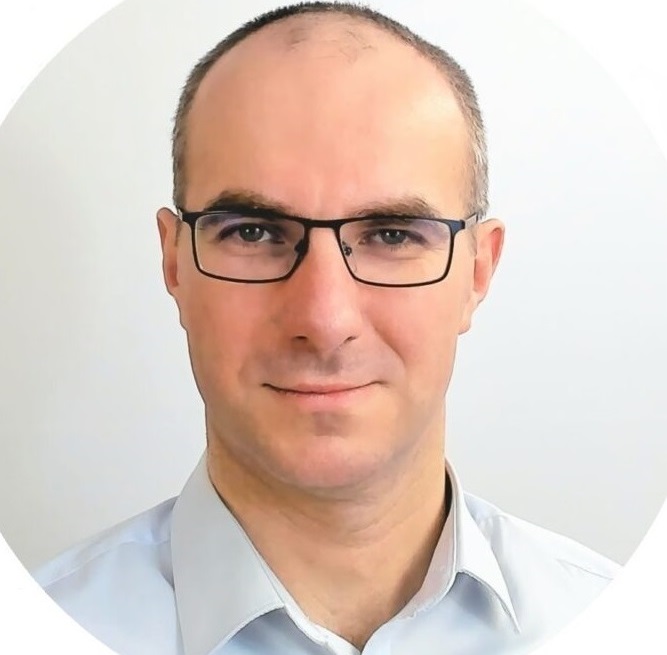
Krzysztof Żarczyński
VALIDATIE INGENIEUR
Verantwoordelijk voor offerte, opstellen van testplan, uitvoeren van metingen, rapporteren van resultaten. Levensmiddelentechnoloog van opleiding. Ervaring opgedaan in kwaliteitsborging en validatie in levensmiddelen- en farmaceutische productiebedrijven.
info@sigma-lab.nl
[taal: Nederlands, Engels, Pools]
+48 530 30 90 30
[taal: Engels, Pools]
PRIJSLIJST
Wilt u snel een schatting van de kosten voor het uitvoeren van metingen?
In de prijslijst vindt u:
– informatie over de metingen die wij verrichten
– prijzen voor enquêtes
- De indeling van schone ruimten kan worden uitgevoerd voor een of meer van de drie fasen van het gebruik van de ruimte, d.w.z.
– “eenmaal gebouwd”,
– “in ruste”,
– “in actie”.
Onder de “as-built”-toestand wordt verstaan een situatie waarin de cleanroom compleet is met alle hulpsystemen/media, maar zonder machines, meubilair, materialen of personeel. De ruimte moet vóór de metingen worden schoongemaakt, aangezien de bouw- en installatiewerkzaamheden vaak niet volgens een “schone norm” worden uitgevoerd. Het is ook een goede gewoonte om het ventilatiesysteem ten minste enkele dagen te laten draaien voordat de metingen worden uitgevoerd.
Onder “in rust” wordt verstaan dat alle productieapparatuur geïnstalleerd is en er geen productieactiviteiten plaatsvinden. De meting van het aantal deeltjes “in rust” moet worden verricht na een korte periode van luchtzuivering, die normaliter geacht wordt minimaal 15-20 minuten te duren na het einde van de productieactiviteiten en nadat het personeel de geclassificeerde ruimte heeft verlaten.
Onder de toestand “in bedrijf” wordt verstaan dat alle apparatuur in een bepaalde modus werkt met een bepaald aantal personeelsleden.
Het aantal deeltjes wordt gemeten overeenkomstig NEN EN ISO 14644-1. Op basis van de norm wordt een bepaling gemaakt:
- aantal meetpunten (afhankelijk van de oppervlakte van de clean room),
- het volume en de tijd van het op elk meetpunt genomen luchtmonster (afhankelijk van de verwachte reinheidsklasse van de cleanroom).
Voor EUGMP klasse A-D ruimten worden deeltjes groter dan 0,5 µm en 5 µm in aanmerking genomen. Voor cleanrooms ISO 7 – ISO 9 volgens NEN EN ISO 14644-1 worden deeltjes groter dan 0,5 µm, 1 µm en 5 µm in aanmerking genomen. Voor cleanrooms ISO 1 – ISO 6 wordt bovendien rekening gehouden met deeltjes groter dan 0,1µm, 0,2µm en 0,3µm, waardoor het gebruik van een laserdeeltjesteller van een hogere klasse vereist is.
Voordat de metingen voor elke kamer worden verricht, moet het volgende worden bepaald:
- – de toestand van de ruimte waarin de meting moet worden verricht (“as built”, “in rust”, “in bedrijf”),
- – ruimte,
- – verwachte schoonmaakklasse van de kamer.
Een terugwinningstest wordt uitgevoerd om te beoordelen in hoeverre een ruimte kan terugkeren naar het oorspronkelijke reinheidsniveau, of naar het reinheidsniveau dat voor een bepaalde reinheidsklasse vereist is, nadat een aanzienlijke hoeveelheid deeltjes (DEHS-substantie) in de lucht is gebracht. Voor het doel van de test worden gewoonlijk voldoende deeltjes in de lucht gebracht om een verontreinigingsniveau te bereiken dat meer dan 100x (eventueel 10x) de limiet van de reinheidsklasse van de ruimte overschrijdt.
Kennis van de regeneratietijd van de ruimte is een zeer goede maatstaf voor de beoordeling van de prestaties van een clean room omdat, in tegenstelling tot informatie over het aantal luchtwisselingen alleen, de bereikte regeneratietijd van de ruimte ook wordt beïnvloed door de vorm van de ruimte, het aantal en de plaats van de luchttoevoer- en -afvoerpunten, het aantal en de plaats van de “obstakels” in de ruimte (machines, muren, enz.).
De regeneratietijd wordt bepaald tijdens de kwalificatie van nieuwe of aangepaste cleanrooms (in de “as-built”- of “at rest”-toestand) of als onderdeel van de periodieke prestatie-evaluatie van de cleanroom. De meting van de regeneratietijd is niet nodig voor ruimtes of zones waar de lucht in één richting doorheen stroomt (bijv. laminaire stromingskamers).
Wij meten de hersteltijd van de ruimte volgens NEN EN ISO 14644-3 punt B.4.
Voordat de metingen voor elke kamer worden verricht, moet het volgende worden bepaald:
- – Niveau waarop de lucht moet worden verontreinigd: 100x (standaard) of 10x
- – Overwogen deeltjesgrootte: >0,3µm (standaard), of >0,5µm
– Plaats van het meetpunt: op het punt bij de uitlaat (standaard) of op het punt in de kamer met het hoogst gemeten aantal deeltjes
De metingen worden verricht met een nauwkeurige differentiaaldruksensor (micromanometer) die geijkt is in het bereik van -500 Pa ÷ +500 Pa. De micromanometer is uitgerust met twee meetpunten, waarvan er één via een pijp (flexibele buis met een buitendiameter van 8 mm) verbonden is met de ruimte met de hogere druk. De andere aansluiting (inclusief het apparaat) bevindt zich in een ruimte met een lagere druk (referentieruimte met een overdruk van 0 Pa). De meting van het drukverschil in de ruimten wordt driemaal tegelijk uitgevoerd en de gemiddelde waarde van de drie metingen wordt als meetresultaat gerapporteerd.
De meting wordt voornamelijk uitgevoerd met behulp van verbinNENgen die voor dit doel permanent in de gebouwen zijn geïnstalleerd. Dit zorgt voor constantheid in de meetomstandigheden en biedt de beste mogelijkheid om de verzamelde gegevens te vergelijken met historische gegevens. Indien de ruimte niet is voorzien van een geschikte aansluiting, is het soms mogelijk een kabel in de deurafdichting (of onder de deur) aan te brengen.
De rookproef (smoke test) in schone ruimten en apparatuur zoals laminaire kamers, wordt uitgevoerd om de richting van de luchtstroom aan te tonen, dode zones zichtbaar te maken en de laminaire stroming te bevestigen. De rooktest wordt uitgevoerd overeenkomstig NEN EN ISO 14644-3, punt B3.
De rooktest kan worden uitgevoerd voor de gehele ruimte of in gebieden die met de klant zijn overeengekomen – kritisch vanwege de activiteiten die er plaatsvinden. De test levert het bewijs dat de lucht in de ruimte voldoende wordt ververst en dat er geen “dode zones” in de ruimte zijn, waar plaatselijk een grotere accumulatie van verontreinigende stoffen zou kunnen plaatsvinden. De test bevestigt ook rechtstreeks of de vereiste luchtverplaatsingsrichting bij deuren of procesopeningen wordt aangehouden, terwijl de bescherming van de betrokken zone tegen besmetting/verontreiniging afhangt van de luchtverplaatsingsrichting.
Tijdens de test wordt rook geproduceerd dicht bij een deur die ruimten met verschillende statische drukken scheidt. De rookpluim moet naar de ruimte met de laagste druk worden gericht. De rook wordt ook in andere delen van de ruimte gebracht om de aanwezigheid van “dode zones” in de ruimte te beoordelen. Als er een goede luchtuitwisseling in de kamer is, blijft de rook niet in de kamer, maar wordt hij efficiënt afgevoerd naar de afzuigroosters.
In het geval van apparatuur met een eenrichtingsluchtstroom (laminaire openingen) zijn rookproeven vooral bedoeld om de laminaire stroming te controleren. Bij de test wordt verwacht dat de rookpluim parallel over de beschermde ruimte loopt, zonder turbulentie. De test is bijzonder nuttig voor een werkplek die is uitgerust met de daar gewoonlijk gebruikte apparatuur, om na te gaan of de hoeveelheid en de opstelling van de apparatuur de luchtbeweging onder de laminaire toevoer niet verstoren.
Wij meten het ventilatievermogen (en het aantal luchtwisselingen in de ruimte) volgens NEN EN ISO 14644-3 punt B.2.2. Het volume van de in de ruimte toegevoerde lucht wordt bepaald met een bolometer (op elk rooster afzonderlijk), d.w.z. de methode aanbevolen door NEN EN ISO 14644-3. Het aantal luchtwisselingen in de ruimte per uur wordt vervolgens berekend door het gemeten totaal van het volume van de toegevoerde lucht te delen door het gemeten volume van de ruimte. Voor metingen met een bolometer moet de barometer het oppervlak van het rooster nauwkeurig bedekken, zodat de klant de afmetingen van de roosters moet bevestigen zodat de balometer voor aankomst met de juiste meetbussen is uitgerust.
Voordat de metingen worden verricht, moet voor elke kamer het volgende worden opgegeven:
- – afmetingen van elk rooster
- – installatiehoogte van het rooster/plafondhoogte (wij meten niet voor plafonds hoger dan 3,5m).
We voeren kwalificaties uit in cleanrooms (Cleanroom) in overeenstemming met de vereisten van GMP, de norm ISO 14644-1 en de norm ISO 14644-3. Als onderdeel van de kwalificatie van de cleanroom voeren we meestal de volgende soorten metingen uit: meting van het aantal vaste deeltjes in de lucht, meting van de integriteit van HEPA-filters, meting van de hersteltijd van de cleanroom, meting van de lineaire luchtsnelheid, volumestroom van de luchtstroom, meting van het aantal luchtverversingen in de ruimte, test voor het visualiseren van de luchtstroomrichting, meting van de overdruk van de cleanroom ten opzichte van aangrenzende zones, meting van temperatuur en vochtigheid in de ruimte, concentratie van CO2 in de lucht. Metingen in cleanrooms kunnen worden uitgevoerd als onafhankelijke studies of als een groep tests die een IQ OQ PQ kwalificatie van de cleanroom vormen (de zogenaamde validatie van cleanrooms).
Installatiekwalificatie (IQ) is onderdeel van de kwalificatie van apparatuur/ installaties en ruimtes (waaronder Cleanroom ruimtes), waarbij wordt bevestigd dat de te kwalificeren installatie of ruimte is gebouwd en geïnstalleerd volgens het goedgekeurde ontwerp en de aanbevelingen van de fabrikant, dat de leveringsomvang overeenkomt met de bestelling (inclusief de documentatie in dit verband – gebruiksaanwijzing, exploitatie-instructies), en dat de belangrijkste elementen van het gekwalificeerde systeem of cleanroom correct zijn geïdentificeerd. De kwalificatie van cleanrooms (Cleanroom) wordt voornamelijk uitgevoerd in bedrijven in de farmaceutische en cosmetische industrie, maar soms vereisen laboratoria ook IQOQPQ-kwalificatie. In tegenstelling tot operationele kwalificatie, is het type tests dat onderdeel is van installatiekwalificatie vaak vergelijkbaar tussen verschillende groepen apparatuur, installaties en systemen. Installatiekwalificatie IQ (inclusief de IQ-kwalificatie van cleanroom Cleanroom) omvat vaak: verificatie van de voltooiing van FAT/SAT, controle van de correctheid/volledigheid van de levering en verificatie van de afwezigheid van schade aan geleverde elementen, identificatie van componenten van het apparaat (fabrikant, type, serienummer, materiaal), verificatie van software, verificatie van de markering van de hoofdelementen van het apparaat/systeem/ruimte, controle van de volledigheid van de technische documentatie (beschrijvingen, instructies, schema’s, diagrammen, resultaten van vaste-deeltjes emissietests voor materialen en apparatuur bestemd voor Cleanroom). Installatiekwalificatie kan ook een beoordeling van het mechanisch ontwerp, een beoordeling van het elektrisch ontwerp, controle van de correctheid van installatie en aansluiting op media (elektriciteit, water, perslucht) omvatten. IQ-testen kunnen ook metingen van milieuomstandigheden omvatten – meestal temperatuur en relatieve luchtvochtigheid. In het geval van kwalificatie van cleanrooms (Cleanroom) kan ook de concentratie van koolstofdioxide (CO2) in de ruimte worden onderzocht. De IQ-kwalificatie kan ook een overzicht van meetinstrumenten en een lijst van reserveonderdelen, een rapport over software-installatie, kalibratiecertificaten van controle- en meetapparatuur omvatten. Zoals bij elke kwalificatie, wordt ook bij de installatiekwalificatie (IQ) gerapporteerd over de personen die de kwalificatie uitvoeren, de voorwaarden en datum van de tests, en worden de meetinstrumenten geïdentificeerd die gebruikt zijn voor de uitvoering van de IQ-kwalificatie (indien van toepassing). Het aantal controles tijdens installatiekwalificatie kan beperkt zijn op voorwaarde dat bepaalde tests tijdens FAT/SAT zijn uitgevoerd. Gewoonlijk is voor het ontwikkelen van een kwalificatieplan voor installatie van een cleanroom passende documentatie nodig (URS, bestelling, P&ID-schema’s, materiaallijsten, specificatiebladen, DTR-apparaat, beschrijving van het gekwalificeerde systeem). GMP geeft aan dat de installatiekwalificatie moet omvatten (minimale vereisten): controle van de correctheid van de montage van apparatuur, instrumenten, apparaten, pijpleidingen en technische installaties in termen van hun overeenstemming met technische tekeningen en specificaties; controle van de juistheid van montage in verhouding tot eerder gedefinieerde criteria; het verzamelen en verifiëren van de door de leverancier verstrekte gebruiksaanwijzingen en exploitatie-instructies, evenals onderhoudsvereisten; kalibratie van instrumenten; verificatie van bouwmaterialen.
Operationele Kwalificatie (OQ) heeft als doel het leveren van objectief bewijs dat de individuele functionaliteiten van de geteste schone ruimte (Cleanroom)/apparatuur/installatie correct functioneren – in overeenstemming met de functionele specificatie FS of binnen het bereik van het geplande gebruik van de apparatuur door de gebruiker. Operationele kwalificatie wordt uitgevoerd na een succesvolle afronding van de installatiekwalificatie (IQ), en kan ook worden uitgevoerd (geheel of gedeeltelijk binnen de oorspronkelijke reikwijdte van de operationele kwalificatie) na reparatie van de apparatuur of de ruimte. De tests die tijdens de operationele kwalificatie worden uitgevoerd, variëren afhankelijk van het type van de gekwalificeerde apparatuur, maar het is mogelijk om bepaalde groepen tests te identificeren die meestal worden uitgevoerd tijdens dit deel van de kwalificatie. Voorbeeld van een OQ-testbereik voor de kwalificatie van een schone ruimte: functionele tests – het bereiken en stabiliteit van kritieke/extreme systeemparameters (bijv. luchtstroomsnelheid onder laminar flow, aantal luchtverversingen in de ruimte, hersteltijd van de ruimte), alarmeringstests (bevestiging van correcte activering en communicatie van alarmen), rapportagegeneratie, toegangscontrole tot verschillende functies door verschillende gebruikersgroepen van de schone ruimte; identificatie van materialen en meetapparatuur gebruikt tijdens de kwalificatie van de schone ruimte (geldigheid van certificaten/kalibratiebewijzen); het feit dat gebruikerstrainingen voor de installatie/schone ruimte zijn uitgevoerd; de aanwezigheid van goedgekeurde instructies en procedures (schoonmaakinstructies, onderhoud, kalibratie).
Het rapport van de kwalificatie moet ook de personen aangeven die de operationele kwalificatie uitvoeren en de datum van uitvoering van de afzonderlijke tests. Om een plan voor operationele kwalificatie van een cleanroom te ontwikkelen, moet men beschikken over de juiste documentatie: functionele specificatie (werkingsbereik van het apparaat/element, doelwaarden van werkparameters), karakteristiekenkaarten en beschrijving van het systeem, DTR. GMP geeft aan dat tests uitgevoerd in het kader van de operationele kwalificatie moeten: worden ontwikkeld op basis van kennis van processen, systemen en apparaten om te bevestigen dat het systeem werkt zoals ontworpen; onder- en bovengrenzen van operationele parameters of de voorwaarden van het ergste geval bevestigen.
De resultaten van metingen uitgevoerd in het kader van de kwalificatie van de cleanroom worden gedocumenteerd in de vorm van afzonderlijke Testkaarten. Een rapport van de kwalificatie van de cleanroom omvat ook: een beschrijving van het doel van de kwalificatiewerkzaamheden, een beschrijving van het gekwalificeerde systeem – systeemgrenzen, een basisbeschrijving van de constructie en werking, kritieke elementen, een vereenvoudigd constructieschema dat de plaatsing van de belangrijkste subeenheden laat zien (voor complexe apparaten en systemen), een lijst van testkaarten, IQ OQ PQ-testkaarten met resultaten van controles en metingen, onregelmatigheden gevonden tijdens de kwalificatie, een samenvatting van de kwalificatie met verwijzingen naar de aangenomen acceptatiecriteria, kopieën van huidige kalibratiecertificaten van meetinstrumenten gebruikt tijdens de kwalificatie van het apparaat, een lijst van personen die deelnemen aan de kwalificatie van het apparaat.
Ons bedrijf voert kwalificaties van cleanrooms uit in bedrijven in de farmaceutische, cosmetische industrie, in laboratoria. We voeren ook kwalificaties van autoclaven, IQOQPQ-kwalificaties van laboratoriumapparatuur, kwalificaties van gecomprimeerde lucht (ISO 8573) uit. We werken ook samen met leveranciers van productieapparatuur, uitvoerders van cleanrooms en leveranciers van laboratoriumapparatuur, die vanwege de noodzaak om de geldigheid van kalibratie van meetinstrumenten gebruikt in kwalificatie te behouden, de uitvoering van sommige of alle metingen willen uitbesteden.
De snelheid en de homogeniteit van de luchtstroom onder het HEPA-filter worden gemeten overeenkomstig NEN EN ISO 14644-3 punt B.2. De meting dient om de correcte werking van de laminaire stroming en de mate van filterslijtage te beoordelen. Een te lage luchtsnelheidswaarde kan het gevolg zijn van aanzienlijke vervuiling (slijtage) van het filter en geeft aan dat het filter moet worden vervangen. Het algemeen aanvaarde aanvaarNENgscriterium (EUGMP) voor de beoordeling van de uniformiteit van de luchtsnelheid onder een HEPA-filter is 0,45 m/s +-20%. Ons bedrijf voert luchtsnelheidsmetingen uit, maar levert geen diensten voor de vervanging en verwijdering van gebruikte HEPA-filters.
HEPA-filterintegriteitstests worden uitgevoerd om te bevestigen dat het filter stevig in de behuizing is geïnstalleerd en geen schade of lekkage vertoont. HEPA-filter integriteitstesten detecteren lekkage van onvoldoende gereinigde lucht, wat kan resulteren:
- – onvoldoende dichtheid van de verbinNENg tussen filter en rooster (bijvoorbeeld door ongelijke druk tussen filter en roosterhuis,
– beschadigde of versleten afdichtingen), - – schade aan het filter tijdens transport of installatie,
- – onjuiste installatie van het filter,
- – het filter te lang gebruiken.
HEPA-filterintegriteitstests worden voornamelijk uitgevoerd voor kritische kwaliteitsruimten en schone zones, bijvoorbeeld in ISO-klasse 5 of ISO-klasse 6 schone ruimten, laminaire openingen in microbiologische laboratoria. Veel gebruikers van cleanrooms voeren geen HEPA-filterintegriteitsmetingen uit in ruimtes van ISO-klasse 7-ISO 8 als deze ruimtes voldoen aan de eisen voor het aantal deeltjes in de lucht.
Wij voeren de integriteitstest van het HEPA-filter uit volgens NEN EN ISO 14644-3, punt B.7.
De meting bestaat uit het inbrengen van een testaërosol vóór het te testen HEPA-filter, het meten van het aantal deeltjes vóór het filter en vervolgens het meten van het aantal deeltjes achter het filter terwijl het oppervlak van het filterframe, de ruimte tussen het frame en de filterbevestigingswanden, het gebied rond de pakking en het gehele filteroppervlak worden gescand met een speciale sonde die is aangesloten op een laserdeeltjesteller.
ISO 14644-3 geeft aan dat bij het testen van de integriteit van filters met een filtratie-efficiëntie ≥99,995% (HEPA 14-filters en hoger), penetratie >0,01% moet worden beschouwd als “lekkage”, terwijl voor filters met een filtratie-efficiëntie ≥99,95% maar minder dan 99,995% (onder andere HEPA 13-filters), penetratie >0,1% moet worden beschouwd als “lekkage”.
Om de testaërosol in de installatie te brengen, wordt de buis met de geproduceerde aërosol aangesloten op het toevoerkanaal vóór het te testen filter (een gat met een diameter van 10 mm of een spie met een buitendiameter van 7 mm is vereist). Om de aërosolconcentratie stroomopwaarts van het filter te meten is een gat met een diameter van 13 mm of een spie met een buitendiameter van 10 mm in de installatie nodig.
Voor ISO klasse 8 schone ruimten worden gewoonlijk verschillende luchtfiltratieniveaus gebruikt (bv. G4 voorfilter, F9 filter, H13 eindfilter). De luchtbeweging in de ruimte is niet-unidirectioneel (er is een vermenging van de “schone” lucht die naar de ruimte wordt toegevoerd met de “vuile” lucht die in de ruimte aanwezig is). De luchtinlaten in een ISO 8 clean room bevinden zich meestal aan het plafond. De lucht wordt gereinigd door een HEPA-filter in het rooster (in het plafond) of door een HEPA-filter in de HVAC-eenheid. De ventilatieopeningen bevinden zich gewoonlijk aan de wanden in de buurt van de vloer (bv. in de hoeken van de ruimte). Het vereiste aantal luchtwisselingen per uur hangt af van de aard van de cleanroomactiviteiten en het aantal aanwezige personeelsleden, maar er kan worden gestreefd naar 10-40 luchtwisselingen per uur. In ISO klasse 8 cleanrooms is het personeel vaak continu aanwezig. Het personeel kan gekleed zijn in standaard werkkleNENg (lange broek, lange mouw, pet) en bezoekers in een wegwerpschort. Aanbevolen wordt een minimale overdruk van 5-10 Pa in de ruimte te handhaven ten opzichte van de aangrenzende zone.
Tijdens de kwalificatie van een ISO klasse 8 clean room worden gewoonlijk de volgende tests uitgevoerd: meting van het aantal deeltjes in de lucht, meting van de regeneratietijd van de ruimte, meting van het drukverschil, meting van de temperatuur en de relatieve vochtigheid. Optionele tests: meting van het aantal luchtwisselingen, integriteitstests van HEPA-filters, rooktest.
Voor cleanrooms van ISO-klasse 7 worden verschillende fasen van luchtfiltratie gebruikt (bv. voorfilter G4, vervolgens filter F9, eindfilter H13 of H14). De luchtbeweging in de ruimte is niet-unidirectioneel. De luchtinlaten in de ISO 7 clean room bevinden zich gewoonlijk aan het plafond (HEPA 13/14 eindfilter bevindt zich in het plafondrooster). De luchtopeningen bevinden zich gewoonlijk aan de wanden in de buurt van de vloer. Het vereiste aantal luchtwisselingen per uur bedraagt vaak 20-60n/u. In ISO klasse 7 cleanrooms is het personeel meestal continu gehuisvest. Het personeel mag gekleed zijn in standaard werkkleNENg (lange broek, lange mouw, pet) en bezoekers in een wegwerpschort. Aanbevolen wordt een minimale overdruk van 10 Pa in de ruimte ten opzichte van de aangrenzende zone te handhaven.
Tijdens de kwalificatie van een ISO klasse 7 clean room worden gewoonlijk de volgende tests uitgevoerd: meting van het aantal deeltjes in de lucht, meting van de hersteltijd van de ruimte, meting van het drukverschil, meting van de temperatuur en de relatieve vochtigheid van de lucht. Optionele tests: meting van het aantal luchtwisselingen, integriteitstests van de HEPA-filters, rooktest.
Voor cleanrooms van ISO-klasse 6 worden verschillende fasen van luchtfiltratie gebruikt (bv. voorfilter F7, vervolgens filter H10, eindfilter H14). De luchtbeweging in de ruimte is niet-unidirectioneel, unidirectioneel (laminair) of gemengd. De luchtroosters in een ISO 6 clean room bevinden zich gewoonlijk aan het plafond (HEPA 13/14 eindfilter bevindt zich in het plafondrooster). De luchtafvoerplenums in een ISO 6 clean room zijn geplaatst op verschillende punten in de ruimte onderaan de wanden. Het vereiste aantal luchtwisselingen per uur ligt vaak in de orde van 40-150 luchtwisselingen /1h. De aanwezigheid van personeel in ISO klasse 6 cleanrooms moet worden beperkt. Personen die ISO klasse 6 ruimten betreden moeten een speciaal cleanroompak of een meerdelige outfit dragen (stofvrij, bijv. polyester – lange broek, lange mouw, handschoenen, kap met nekbescherming, masker, speciaal schoeisel). Aanbevolen wordt om onder de bovenlaag speciaal cleanroomondergoed te dragen. De overdruk van de ruimte ten opzichte van de aangrenzende zone is minimaal 10 Pa.
Tijdens de kwalificatie van een ISO klasse 6 cleanroom worden gewoonlijk de volgende tests uitgevoerd: meting van het aantal luchtwisselingen, HEPA-filter integriteitstests, meting van het aantal deeltjes in de lucht, meting van de regeneratietijd van de ruimte of de luchtsnelheid onder het filter, meting van het drukverschil, meting van de temperatuur en de relatieve vochtigheid, rooktest.
Voor ISO klasse 5 cleanrooms worden verschillende fasen van luchtfiltratie gebruikt (bv. voorfilter F7, dan filter H10, eindfilter H14). De luchtbeweging in de ruimte is meestal eenrichtingsverkeer (laminair). De lucht wordt aangevoerd via roosters in het plafond (minder vaak aan de muur). De meerdere luchtafzuigers in een ISO 5 cleanroom zijn meestal onderaan de wanden of in de vloer geplaatst (of op de tegenoverliggende wand bij gebruik van horizontale roosters). Voor cleanrooms met laminaire luchtstroom is de sleutel niet het aantal luchtwisselingen per uur, maar de waarde van de lineaire luchtsnelheid onder het filter. Meestal wordt gestreefd naar een stroomsnelheid van 0,45 m/s +/- 20 %. De aanwezigheid van personeel in een ISO klasse 5 cleanroom is slechts in uitzonderlijke omstandigheden aanvaardbaar. Personen die een ISO-klasse 5 cleanroom betreden, moeten zich kleden in een speciaal cleanroompak of een meerdelige outfit (stofvrij, bijv. polyester – lange broek, lange mouwen, handschoenen, kap met nekbeschermer, masker, speciaal schoeisel). Aanbevolen wordt om onder de bovenlaag speciale cleanroomonderkleNENg te dragen. De overdruk van de ruimte ten opzichte van de aangrenzende zone is minimaal 10 Pa.
Tijdens de kwalificatie van een ISO klasse 5 cleanroom worden gewoonlijk de volgende tests uitgevoerd: meting van het aantal luchtwisselingen, HEPA-filter integriteitstests, meting van het aantal deeltjes in de lucht, meting van de regeneratietijd van de ruimte of de luchtsnelheid onder het filter, meting van het drukverschil, meting van de temperatuur en de relatieve vochtigheid, rooktest.
Bij het ontwerpen van cleanrooms is het van cruciaal belang om een grondig ontwerpproces te doorlopen, technisch-organisatorische afspraken te maken die als leidraad dienen voor de realisatie van de cleanroom, bouw- en installatiewerkzaamheden uit te voeren op basis van een goedgekeurd en geverifieerd cleanroomontwerp, nauwgezette acceptatieprocedures volgens ISO 14644 uit te voeren, de bedrijfsvoorschriften van de cleanroom vast te stellen en na te leven, en onderhoud op een functioneel veiligheidsniveau te houden (gebaseerd op functionaliteitsindicatoren afhankelijk van het doel van de cleanrooms). De samenwerking tussen de ontwerper, de investeerder en de expert in ISO 14644-1, evenals de kwaliteitsborging (QA) door het gehele plannings-, bouw-, acceptatie- en gebruiksproces van de cleanroom, is van groot belang.
Het ontwerp van ventilatie- en airconditioningsystemen voor cleanrooms moet overeenkomen met de vereisten die voortvloeien uit de architectuur, de binnen de cleanroom gebruikte technologieën, de indeling van de ruimtes, de scheiding van de cleanroom van de niet-cleanroom gebieden en de interne communicatie. Ventilatie- en airconditioningsystemen in cleanroomfaciliteiten moeten zorgen voor:
– Luchtreinheid op het vereiste niveau, bepaald door de toelaatbare concentratie van verontreinigingen zoals vaste deeltjes en micro-organismen, afhankelijk van het type en de functie van de ruimtes, met bijzondere aandacht voor de eisen aan de cleanroom,
– Voorkomen van luchtgedragen verontreinigingstransport door een vereiste luchtstroomrichting tussen ruimtes (cascadesysteem van luchtdruk), waarbij de luchtstroom van ruimtes met hogere luchtkwaliteitseisen naar ruimtes met lagere eisen gaat, het handhaven van de juiste snelheid van toegevoerde lucht, het afvoeren van interne warmte- en vochtwinsten door voldoende geconditioneerde lucht aan te voeren vanuit de airconditioningscentrale (ventilatiesysteem), en het waarborgen van comfortabele omstandigheden voor het personeel door de vereiste thermisch-hygienische omstandigheden in de ruimtes te handhaven.
Het naleven van de ISO 14644-1 norm en het implementeren van hoogwaardige cleanroom en ventilatiesystemen zijn essentieel voor het waarborgen van de functionaliteit en veiligheid van cleanrooms.
Voor een efficiënt ventilatie- en afzuigsysteem in een Cleanroom ISO 8 zijn de basisvereisten als volgt:
– Aanbevolen luchtdrukopbouw: een overduk van minimaal 10Pa.
– Gebruik van zeer effectieve filters van ten minste klasse H12.
– De snelheid van de luchtstroom op 0,30 m onder het luchtuitlaatoppervlak moet tussen 0,20 – 0,45 m/s liggen.
– De uitgevoerde luchtstroom moet voldoende zijn om de warmte- en vochtwinst te balanceren; deze mag niet minder zijn dan 50% van de toegevoerde buitenluchtstroom.
– De minimale luchtverversingsfrequentie: 15 verversingen/uur.
In bijzondere gevallen, afhankelijk van het gebruik van de ruimte, de uitgevoerde functies en bij afwezigheid van specifieke wettelijke eisen, dient de toewijzing van cleanrooms aan een specifieke stofreinheidsklasse volgens ISO 14644-1 vastgesteld te worden in overleg tussen de investeerder, kwaliteitswaarborging, de aannemer, en indien nodig een bouwdeskundige, en bevestigd te worden met een schriftelijk document bijgevoegd aan de projectdocumentatie.
De ventilatieluchtstroom moet worden bepaald op basis van de balans van warmte- en vochtwinst of verontreinigingsconcentraties. De opgegeven minimale luchtverversingsfrequenties dienen als richtlijnen en mogen niet de enige basis zijn voor het ontwerpen van ventilatie- en airconditioningsystemen voor Cleanrooms, maar dienen slechts als indicatie van het vereiste minimum voor de betreffende cleanroomklasse.
Indien niet anders overeengekomen, dient de stofreinheidsklasse ISO 14644-1 bepaald te worden op basis van de productieprocessen uitgevoerd door andere entiteiten met een vergelijkbaar productieprofiel en dient de oplossing door de investeerder te worden goedgekeurd.
Voor het ontwerpproces van het ventilatie- en airconditioningsysteem, met name voor ruimtes van klasse ISO 5 en lager, moet de investeerder schriftelijk de geplande operaties in de cleanrooms en de geplande cleanroomuitrusting specificeren. De technologische eisen voor een cleanroom ISO 5 en schoner moeten definitief worden vastgesteld na overleg met het personeel van de investeerder en kwaliteitswaarborging.
Aanbevelingen voor ventilatie en airconditioning voor Cleanrooms:
Ruimtes en gebieden geclassificeerd als ISO 5-9 moeten zijn uitgerust met mechanische aan- en afvoerventilatie- en airconditioningsystemen die ten minste de minimale luchtverversingsfrequentie, de vereiste luchtreinheid en thermisch comfort bieden, zonder de noodzaak om de relatieve vochtigheid aan te passen. Het primaire doel van het ventilatie- en airconditioningsysteem in een cleanroom is het handhaven van de luchtkwaliteit, wat wordt bereikt door:
– Het handhaven van een positieve luchtdruk ten opzichte van aangrenzende ruimtes,
– De aanvoer van schone lucht met een specifieke, constante snelheid en een specifiek temperatuurverschil tussen de toevoertemperatuur en de daadwerkelijke temperatuur in de ruimte binnen een bereik van 1-3 K,
– Het verdunnen van verontreinigingen door het aanvoeren van een passende hoeveelheid buitenlucht van de vereiste reinheid.
Voor veel cleanrooms wordt het gebruik van een aanvoersysteem met plafondroosters of een volledig laminaar plafond met lage turbulentie aanbevolen, met behoud van de vereiste dalingsnelheid van de luchtstroom. In de beschermde zone van cleanrooms moet een passende luchtverversingsfrequentie worden gewaarborgd om thermisch comfort, de vereiste overduk en een unidirectionele luchtstroom uit de ruimte naar aangrenzende ruimtes te garanderen via deuren of andere technologische elementen.
Het wordt aanbevolen om de mogelijkheid te overwegen om de hoeveelheid toegevoerde lucht te verminderen (tot minimaal 50% van de nominale toevoerluchtstroom) wanneer de cleanroom niet in gebruik is. Het uitschakelen van het ventilatie- en airconditioningsysteem tijdens pauzes in het gebruik van cleanrooms, met name ISO 7 en lager, wordt niet aanbevolen. In geen geval mag de luchtstroomrichting tussen ruimtes worden omgekeerd door het verlies van overduk ten opzichte van aangrenzende ruimtes.
Na het uitschakelen van het ventilatie- en airconditioningsysteem dat de cleanroom bedient, is het noodzakelijk om het systeem opnieuw te activeren in voldoende tijd (minimaal 60 minuten) vóór de start van de volgende productieactiviteiten of om ten minste 30 luchtverversingen (met betrekking tot verse lucht) in de ruimte te waarborgen voordat het in gebruik wordt genomen.
Om downtime van systemen die cleanrooms bedienen, wat een risico kan vormen voor de productieactiviteiten in de cleanroom, te vermijden, wordt het gebruik van redundante apparatuur (of ten minste een redundant ventilatorontwerp) aanbevolen, uitgerust met een besturings- en automatiseringssysteem dat hun automatische activering in geval van falen van de primaire apparatuur mogelijk maakt, te worden bestuurd vanuit de cleanroom.
Voor de verwarming van cleanrooms wordt het gebruik van oppervlakteverwarming aanbevolen. Het gebruik van verwarmingsapparaten met gladde, niet-geribbelde verwarmingsoppervlakken die gemakkelijk te reinigen en te desinfecteren zijn (bijvoorbeeld radiatoren in een hygiënische uitvoering) is toegestaan. Luchtstroom veroorzaakt door de behoefte aan thermisch comfort in het gebied van de cleanroom mag de laminaire luchtstroom niet verstoren (in cleanrooms met een unidirectionele luchtstroom). Bij twijfel wordt aanbevolen een visualisatie van de luchtstroom (rooktest) uit te voeren, bijvoorbeeld volgens ISO 14644-3.
Voor het aanbrengen van de afwerkingslagen in de cleanroom (muren, plafonds, vloeren, deuropeningen, enz.) moet een grondige inspectie van de gehele bouw- en installatiestructuur worden uitgevoerd en moeten alle openingen en andere elementen die lekkage van de ruimte kunnen veroorzaken, worden afgedicht met materialen die geschikt en toegestaan zijn voor gebruik in cleanrooms (ISO 14644-14). Leden van de inspectiecommissie moeten onder andere de investeerder en/of gebruiker, de aannemer en de bouwtoezichtinspecteur omvatten. De luchtdichtheid van de ruimte moet worden bevestigd met een geschikt protocol, ondertekend door alle leden van de commissie.
Vóór de installatie van de uiteindelijke ventilatiecomponenten (d.w.z. laminaar plafond, mengventilatie-uitlaten, afzuigroosters, dempers, debietregelaars) moeten definitieve dichtheidstests van de toevoer- en recirculatie-installaties worden uitgevoerd in aanwezigheid van een vertegenwoordiger van de investeerder en/of gebruiker en de bouwtoezichtinspecteur gespecialiseerd in sanitaire voorzieningen. In bijzondere gevallen wordt aanbevolen om een validatiespecialist of HVAC-expert als extra lid van de commissie te hebben.
De meting van de overduk tussen ruimtes moet onder het verlaagde plafond worden uitgevoerd. In alle cleanrooms die met overduk worden beschermd, moet bovendien een overduk tussen de ruimte en de ruimte boven het verlaagde plafond worden gewaarborgd.
In cleanrooms met de hoogste hygiënische eisen (ISO 5 en schoner) wordt doorgaanseen laminaire luchtstroom gebruikt. De toegevoerde luchtstroom moet, naast het waarborgen van de juiste snelheid van de toegevoerde lucht en de juiste temperatuur, ook de warmte- en vochtwinst verwijderen met behoud van het vereiste overduk ten opzichte van aangrenzende ruimtes.
Cleanrooms van ISO 5 vereisen meestal een drietraps luchtfiltratiesysteem voor de toegevoerde lucht en een eenfasige filtratie voor de afgevoerde lucht. De minimale vereisten voor de luchtfilters van de toegevoerde lucht zijn als volgt:
- 1e trap: filter van klasse F7,
- 2e trap: filter van klasse F9,
- 3e trap: filter van klasse H13.
In gebieden met hoge vervuiling van de buitenlucht, in geïndustrialiseerde en grote steden, moet het F7-filter voorafgegaan worden door een groffilter.
Voor de filtratie van de afgevoerde lucht moeten filters van minimaal klasse M5 en deeltjesscheiders op de afvoerroosters met een maaswijdte van niet meer dan 0,8 mm gebruikt worden. De afvoerroosters aan de wand moeten zo gelijkmatig mogelijk in de ruimte verdeeld worden om de stabiliteit van de laminaire stroom te waarborgen, bijvoorbeeld door ze in elk van de vier hoeken van de ruimte of in de buurt daarvan te plaatsen, met twee roosters op één locatie – één dicht bij het plafond en de ander dicht bij de vloer. Er moet 20% van het luchtvolume uit het plafondgebied (via roosters geplaatst tot 0,30 m onder het plafondoppervlak) en 80% van het luchtvolume uit het vloergebied (op een hoogte tot 0,30 m boven de vloer) verwijderd worden. De locatie van de bovenste afvoerroosters mag het direct aanzuigen van toegevoerde lucht (het zogenaamde kortsluiteffect) niet veroorzaken. Het wordt aanbevolen om een oplossing te gebruiken die individuele luchtstroomregeling voor de bovenste en onderste afvoerroosters mogelijk maakt, bijvoorbeeld door het gebruik van regelkleppen of roosters met ingebouwde regelkleppen.
De direct afgevoerde luchtstroom tijdens de werking van het systeem mag niet minder zijn dan 50% van de toegevoerde buitenlucht, waarbij de afgevoerde luchtstroom voor de selectie van afvoerroosters niet minder dan 90% van de toegevoerde luchtstroom moet zijn.
Om de vereiste luchtkwaliteit in cleanrooms van ISO 5 tot ISO 8 te waarborgen, is het gebruik van een sluis noodzakelijk. In de sluis moet een onderdruk ten opzichte van de cleanroom en een overduk ten opzichte van aangrenzende ruimtes gehandhaafd worden. Het overvloedige compensatielucht moet systematisch worden afgevoerd (bijvoorbeeld via overdrukventielen) of door een spleet onder de deur. De luchttoevoer naar de sluis moet gebeuren via toevoerroosters in een hygiënische uitvoering met een hoogefficiënt filter van minimaal klasse H13, waarbij een passende luchtverversingsfrequentie gewaarborgd moet worden.
Als een luchtbevochtiger wordt gebruikt in de toevoerinstallatie, moet er een filter van ten minste klasse F7 voor worden geplaatst.
Wanneer cleanrooms van klasse ISO 8 of ISO 9 niet in gebruik zijn, mag het mechanische ventilatiesysteem worden uitgeschakeld, maar het moet nog 60 minuten na het verlaten van de ruimte door het productiepersoneel werken en 30 minuten voor de start van de productie worden ingeschakeld.
Voor cleanrooms van de ISO 8 klasse, ongeacht de externe omstandigheden, wordt aanbevolen de volgende ontwerpparameters voor het binnenklimaat aan te nemen:
– De luchttemperatuur regelbaar binnen het bereik van 19-23°C,
– De relatieve vochtigheid binnen het bereik van 30-65%.
Bij specifieke productietechnologische vereisten in de cleanroom, die niet in deze richtlijnen zijn opgenomen, kunnen andere temperatuur- en vochtigheidswaarden worden aangenomen. In dergelijke gevallen moeten eventuele afwijkingen van bovenstaande waarden worden overeengekomen tussen de ontwerper, investeerder, en een bouwexpert op het gebied van ventilatie en airconditioning. Het toepassen van andere parameterwaarden in het ontwerp moet worden gerechtvaardigd of gedocumenteerd (bijvoorbeeld in het geval van speciale eisen gerelateerd aan de gebruikte apparatuur of specifieke procesvereisten).
Voor cleanrooms moet de temperatuur van de aangevoerde lucht in overeenstemming zijn met de aanbevelingen van de fabrikant van de luchttoevoerroosters en tegelijkertijd thermisch comfort in de cleanroom waarborgen. Ventilatie- en airconditioningsystemen moeten een vereist niveau van relatieve luchtvochtigheid garanderen door gebruik te maken van adequaat ontworpen luchtbevochtigings- en ontvochtigingssystemen. In de winter mag de relatieve luchtvochtigheid in een cleanroom van klasse ISO 8 niet lager zijn dan 30%, terwijl deze in de zomer niet meer dan 65% mag bedragen.
Voor cleanrooms van lagere klassen wordt een ontwerpluchttemperatuur binnenshuis van 21°C voor de winter en 23°C voor de zomer aanbevolen. Voor deze klassen van ruimtes is het niet noodzakelijk om systemen met regelbare relatieve luchtvochtigheid te gebruiken, maar het wordt aanbevolen oplossingen te gebruiken die het mogelijk maken om deze binnen het bereik van 30-65% te houden.
Om de juiste luchtdrukcascade in cleanrooms te handhaven, moeten de volgende eisen worden vervuld:
– De luchtdrukverschil tussen de cleanroom en alle aangrenzende ruimtes moet ten minste 10 Pa zijn,
– Het luchtdrukverschil tussen de hulpruimte en de gang moet ten minste 5 Pa zijn,
– Het luchtdrukverschil tussen de schone gang en de vuile gang moet ten minste 5 Pa zijn.
Voor alle cleanrooms wordt aanbevolen een over-/onderdruk van lucht te handhaven met een waarde van niet minder dan 10 Pa ten opzichte van de sluis.
In geval van een bijzonder risico moet in de cleanroom een luchtdrukcascade van minimaal 15 Pa overduk tussen de ruimte en de sluis, en minimaal 5 Pa tussen de sluis en de gang worden gewaarborgd. In alle ruimtes wordt aanbevolen om een hoger luchtdrukverschil dan de minimale waarden te handhaven, echter zonder de maximale toelaatbare geluidsniveau A in de geanalyseerde ruimtes te overschrijden.
Het is niet toegestaan ruimtes met een verschillende functie en verschillend luchtdrukschema binnen één ruimte te combineren.
Het vereiste over-/onderdruk van lucht moet absoluut gehandhaafd blijven tijdens elke fase van de werking van de installatie, ongeacht de vervuiling van filters, de werkingsmodus (volledige of beperkte capaciteit), en andere storingen in het ventilatie- en airconditioningsysteem. Het besturings- en automatiseringssysteem dat toezicht houdt op de juiste werking van de ventilatie- en airconditioningsystemen moet rekening houden met de bovengenoemde vereisten.
Bij het ontwerpen van systemen voor cleanrooms is het essentieel om ervoor te zorgen dat de luchttemperatuur nabij de luchtfilters hoger is dan het dauwpunt, ook tijdens inactieve perioden van het systeem. De constructie van de frames en cassettes van de filters moet de groei van micro-organismen voorkomen, eenvoudige en veilige montage mogelijk maken en de dichtheid van het gemonteerde filter waarborgen. Filters moeten direct na productie vrij zijn van materialen die tijdens de werking van het systeem kunnen vrijkomen. Filtermaterialen mogen niet met biociden zijn geïmpregneerd. De behuizingen van filters van de eerste en tweede trap moeten gemaakt zijn van vochtbestendige materialen die niet vervormen tijdens montage en gebruik. Bij levering moeten de filters ten minste aan een voorlopige inspectie worden onderworpen om schade of vervuiling, evenals de staat van de op hen gemonteerde afdichtingen (binnen het montagebereik van het filterelement), te detecteren. Het filtermateriaal mag geen zichtbare vervuiling of schade vertonen. Filters moeten in veilige verpakkingen worden verpakt om het filtermateriaal tegen beschadiging en de afdichtingen tegen kneuzingen te beschermen.
Elke filtersectie in de HVAC-centrale moet zijn uitgerust met een drukschakelaar of druktransmitter (om filtervervuiling te controleren). Het wordt aanbevolen dat alle hoogefficiënte filters (of groepen filters op plaatsen met identieke hydraulische en gebruikskarakteristieken) die direct in de luchttoevoerroosters zijn geplaatst, zijn uitgerust met een drukschakelaar of druktransmitter. Deze apparaten moeten samenwerken met een specifiek besturings- en automatiseringssysteem dat de werking van de toevoer-, afvoer- en recirculatie-installatie beheert. Voor apparatuur die cleanrooms van klasse ISO 8 en hoger bedient, is daarnaast de mogelijkheid van lokale aflezing van de instellingen van de drukschakelaar of druktransmitter vereist, naast het gebruik van overkoepelende besturingssystemen van de operatieblok of het BMS-druksysteem. Technisch personeel moet de datum van elke filtervervanging documenteren, met vermelding van het type en de grootte van het filter.
De exploitatie van cleanrooms van klasse ISO 8 en hoger uitgerust met beschadigde of niet goed gemonteerde HEPA-filters kan leiden tot een verhoogd risico op infecties en een direct gevaar vormen voor de productieprocessen die daarin worden uitgevoerd.
Montage en vervanging van filters van de eerste en tweede trap
Het filter van de eerste en tweede trap moet worden vervangen als de luchtdrukval groter is dan of gelijk is aan de maximale waarde aanbevolen door de fabrikant. Het is noodzakelijk om een luchtdichte verbinding tussen het filterframe en de behuizing van de unit te verzekeren. Voor afdichting wordt het gebruik van ondoorzichtige afdichtingsmaterialen of geprefabriceerde afdichtingen van materiaal met gesloten poriën, goedgekeurd voor gebruik in installaties met verhoogde hygiënische eisen, aanbevolen. De eerste filtervervanging in de HVAC-centrale moet worden uitgevoerd na de eerste opstart van de installatie en het uitvoeren van acceptatietesten. Filtervervanging moet vanaf de vuile kant worden uitgevoerd.
Montage en vervanging van HEPA-filters
HEPA-filters moeten worden geleverd met een kwaliteitscertificaat van het filter. Het wordt aanbevolen filters in veilige verpakkingen te bewaren tot aan de montage. Het optreden van lekken op HEPA-filters moet absoluut worden uitgesloten. Mogelijke lektypen omvatten: lekken op het filter, lekken op de verbinding van het filterframe met het constructie-element van de luchttoevoer, lekken tussen het filterframe en het filtermateriaal, lekken tussen het filterframeen het ventilatiekanaal. Het is noodzakelijk om een luchtdichte verbinding tussen het filterframe en de behuizing van de luchttoevoer te garanderen. Voor afdichting wordt het gebruik van geprefabriceerde afdichtingen van materiaal met gesloten poriën aanbevolen, die bestand zijn tegen vocht en schimmels, en geschikt zijn voor gebruik in cleanrooms. In bijzondere gevallen is het gebruik van ondoorzichtige afdichtingsmaterialen die geschikt en toegestaan zijn voor gebruik in cleanrooms toegestaan. De vervanging van een HEPA-filter kan vanaf de kant van de cleanroom worden uitgevoerd. Om de gereedheid van cleanrooms van klasse ISO 8 en hoger voor gebruik te bevestigen, moeten na elke vervanging van HEPA-filters de volgende tests worden uitgevoerd (conform de methodologie volgens ISO 14644-3):
– Uitvoering van een test voor luchtpartikelreinheid (validatie van de ruimte),
– Onderzoek naar de afdichting en integriteit van de hoogefficiënte filters (beoordeling van de uniformiteit van het filtermateriaal),
– Meting van de luchtdrukcascade tussen de ruimtes,
– Meting van de luchtdrukval over het hoogefficiënte filter.
Voor cleanrooms van klasse ISO 8 wordt na elke vervanging van HEPA-filters ook aanbevolen om metingen van de microbiologische luchtreinheid uit te voeren. Een negatief testresultaat kan (maar hoeft niet noodzakelijkerwijs) duiden op onregelmatigheden in de werking van het ventilatiesysteem. Na het installeren van hoogefficiënte filters in de luchttoevoer in cleanrooms van klasse ISO 8, 7, 6, 5, moet een lektest worden uitgevoerd om eventuele schade tijdens de montage en de juistheid van de installatie te beoordelen (beoordeling van de uniformiteit van het filtermateriaal).
De aanbevolen gebruiksduur van een HEPA-filter is 2 jaar, maar deze kan worden verlengd tot 4 jaar, op voorwaarde dat jaarlijks (na de vermelde 2 jaar) de volgende tests en metingen worden uitgevoerd (volgens de methodologie beschreven in EN ISO 14644-3):
– Onderzoek naar de afdichting en integriteit van de hoogefficiënte filters (beoordeling van de uniformiteit van het filtermateriaal),
– Meting van de luchtdrukcascade tussen de ruimtes,
– Meting van de luchtdrukval over het filter.
Deze procedures zorgen ervoor dat cleanrooms hun hoge standaard van contaminatiecontrole behouden, essentieel voor het beschermen van de processen en producten binnen deze gecontroleerde omgevingen.
De projectdocumentatie voor een cleanroom omvat een bouwkundig ontwerp en een uitvoeringsontwerp voor het ventilatie- en airconditioningsysteem, aangevuld met een automatiseringsontwerp voor dit systeem. Dit zorgt voor een integrale aanpak die alle aspecten van de bouw en werking van een cleanroom omvat.
Bouwkundig ontwerp
Het bouwkundig ontwerp dient als basis voor de bouwwerkzaamheden en wordt aangevuld met een technische specificatie die op maat is gemaakt voor de uitvoering en acceptatie van het werk. Dit document moet een gedetailleerde beschrijving bevatten van de toegepaste oplossingen in de cleanroom, waaronder luchtstroomparameters, drukverschillen, en energiebehoeften.
Uitvoeringsontwerp voor ventilatie en airconditioning
Het uitvoeringsontwerp omvat een technische beschrijving, tekeningen en een gedetailleerde specificatie van apparatuur en installatie-elementen. Het moet gedetailleerde berekeningen bevatten voor externe en interne luchtparameters, verwarmings- en koelingsfactoren, en de luchtdrukcascade tussen ruimtes. Het ontwerp moet ook informatie bevatten over de keuze van apparatuur, de dichtheidsklasse van ventilatiekanalen, en specifieke eisen voor het automatiseringssysteem van de installatie.
Automatiseringsontwerp voor ventilatie en airconditioning
Het automatiseringsontwerp moet gedetailleerde schema’s bevatten van de automatische regelingssystemen, inclusief instructies voor gebruik en technische specificaties van de apparatuur. Voor cleanrooms van klasse ISO 5 moet dit een apart document zijn dat technische schema’s, informatie over gebruikte componenten, en een gedetailleerde beschrijving van alle functies omvat die door het automatiseringssysteem moeten worden uitgevoerd.
Uitvoeringsdocumentatie
De uitvoeringsdocumentatie moet een bijgewerkte versie van het uitvoeringsontwerp zijn, inclusief alle wijzigingen die tijdens de bouw zijn aangebracht. Het moet ook de nodige certificaten, technische goedkeuringen en conformiteitsverklaringen bevatten. Daarnaast moet er een lijst van gebruikte apparatuur met technische en operationele documentatie en gebruiksaanwijzingen worden bijgevoegd.
Uitvoeringsdocumentatie voor automatisering
De automatiseringsdocumentatie moet als een afzonderlijk document bij de uitvoeringsdocumentatie worden gevoegd. Het moet schema’s van de gerealiseerde automatische regelingssystemen bevatten, samen met een beschrijving van de werking van het automatiseringssysteem en de principes van werking onder normale en noodomstandigheden. Instructies voor het personeel met betrekking tot de beschikbare werkmodi, temperatuur- en vochtigheidsregeling, en signalering van de correcte werking van het systeem moeten ook worden opgenomen.
Elke belangrijke wijziging in de uitvoeringsdocumentatie ten opzichte van het uitvoeringsontwerp moet worden goedgekeurd door de verantwoordelijke personen, waarbij speciale aandacht moet worden besteed aan het selecteren van apparatuur en het definiëren van functies die door het automatiseringssysteem moeten worden vervuld. Dit zorgt ervoor dat de cleanroom voldoet aan de gestelde eisen en functioneert volgens de verwachtingen, waarbij de veiligheid en effectiviteit van de processen binnen de cleanroom worden gewaarborgd.
Alle betrokken partijen, waaronder de investeerder, het ontwerpteam, en de uitvoerende aannemers, spelen een cruciale rol in het waarborgen van de integriteit en functionaliteit van de cleanroom door middel van nauwgezette aandacht voor de projectdocumentatie. Dit proces verzekert dat de uiteindelijke constructie niet alleen voldoet aan de initiële ontwerpspecificaties, maar ook flexibel genoeg is om aanpassingen en upgrades te accommoderen als reactie op veranderende operationele behoeften of technologische vooruitgang.*Communicatie en Documentatie
Effectieve communicatie tussen alle betrokken partijen en nauwkeurige documentatie van elke stap van het proces zijn van vitaal belang. Dit omvat het bijhouden van wijzigingen in het ontwerp, goedkeuringen, en feedback loops tijdens de bouwfase en de implementatie van het automatiseringssysteem. Door het onderhouden van een dynamisch en interactief documentatieproces, kunnen de teams anticiperen op en snel reageren op eventuele uitdagingen of afwijkingen van de oorspronkelijke plannen.
Kwaliteitscontrole en Validatie
Naast het ontwerp en de uitvoering is kwaliteitscontrole en validatie van essentieel belang voor de succesvolle implementatie van een cleanroomproject. Dit omvat het testen van materialen en apparatuur, het verifiëren van de prestaties van het ventilatie- en airconditioningsysteem, en het valideren van de cleanroom volgens internationale normen zoals ISO 14644. De uitvoeringsdocumentatie moet gedetailleerde verslagen bevatten van deze tests en validaties, inclusief resultaten, conclusies, en eventuele aanbevolen correctieve maatregelen.
Onderhoud en Toekomstige Aanpassingen
De projectdocumentatie moet ook richtlijnen bevatten voor het onderhoud en beheer van de cleanroom, evenals procedures voor toekomstige aanpassingen of upgrades van het systeem. Dit zorgt ervoor dat de cleanroom efficiënt blijft werken en kan evolueren om te voldoen aan nieuwe eisen of standaarden zonder de kernfunctionaliteit te ondermijnen. Het opnemen van een gedetailleerd onderhoudsschema, lijsten van vervangingsonderdelen en materialen, en instructies voor het gebruik van het automatiseringssysteem zijn cruciaal voor de langetermijnprestaties en duurzaamheid van de cleanroom.
Slotbeschouwing
De complexiteit van het ontwerpen, bouwen en onderhouden van een cleanroom vereist een multidisciplinaire aanpak, waarbij de projectdocumentatie dient als de ruggengraat van het gehele proces. Door gedetailleerde en nauwkeurige documentatie te handhaven, kunnen projectteams efficiënter werken, risico’s minimaliseren, en zorgen voor naleving van de hoogste normen voor cleanroomprestaties. Dit documentatieproces speelt een cruciale rol in het waarborgen van de veiligheid, effectiviteit en betrouwbaarheid van de cleanroom gedurende de gehele levenscyclus.
sigma-lab.nl is een merk dat eigendom is van Biuro Naukowo-Techniczne SIGMA, Jezycka 44a/5, 60-865 Poznan, Polen.
VAT ID: PL6661925548
Kontakt
-
Email: info@sigma-lab.nl
[taal: Nederlands, Engels]
Telefoon:
+48 530 30 90 30
[taal: Engels, Pools]